This article focuses on using the 6M tool as a support of the design of an aseptic isolator. The objective is to provide a generic assessment of the machine requirements to ensure that all key aspects are taken into account, and common mistakes are avoided. Thus answering the question: How to design an aseptic processing isolator using 6M?
Ishikawa fishbone diagram and 6M tool are very well-known methods that quality departments often use to investigate an event’s root cause. In manufacturing, we use these tools in case of process deviations, like a failed in-process test. Tools like these are very versatile, and you can adopt them in any department to investigate the source of an unexpected result. Ishikawa’s fishbone diagram is a cause/effect diagram that makes it suitable to analyze the logic of any process. If it is true that this tool is used to find the cause of an error, it is also true that it can be used positively as an error prevention tool.

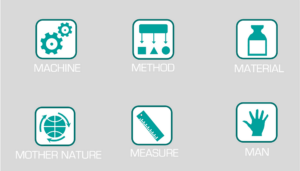
1. Machine
The primary scope of an isolator is to create a contained, aseptic environment in which the process is protected and can be performed with virtually no risk of contamination. Therefore, the isolator needs to be mechanically integrated with the main machine responsible for the process. Moreover, in an aseptic filling line, the isolator will also be connected to an upstream machine and a downstream processing machine.
Besides mechanical integration, communication and integration of process automation between the machines are crucial for the process’s correct functioning.

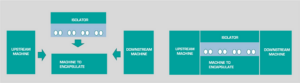
Figure 2 – Schematic example of mechanical integration of machines in a sterile filling line.
The following points need to be considered to identify the specific isolator requirements in relation to the machine:
1. Compatibility of the encapsulated machine/s with isolator design
- Decontamination requirements (consider the presence of occluded/masked surfaces that can limit the sporicidal action of H2O2 vapor)
- Airflow requirements (consider the presence of parts that can disturb the linear airflow and create turbulence)
2. Type of filling machine to encapsulate
- Multiple products vs. campaigned dedicated (impact on changeover activity)
- Small batches vs. large batches (impact on the quantity of consumables inside the isolator and materials to bring in to sustain the process)
- Disposable/dedicated fill set vs. CIP/SIP (impact on parts to transfer inside the isolator)
3. Integration of additional machines and communication
- Pressure cascade implications between the machines
- Logic of sterilization/decontamination of the isolator and upstream machine
- Management of the sterile bit of the isolator
- Physical communication mouseholes and sealing gates between isolator and downstream machine (consider the choice of manual or automatic, active or passive mousehole)
4. Integration of machine interface
- Soft integration (every machine equipped with its HMI from the supplier)
- Hard integration (all the machines share the same HMI of the client)
5. Integration of smaller equipment
- Automatic environmental monitoring (particle counters, vacuum pumps)
- Glove integrity testers
- Decontamination units (location of vapor hydroxide peroxide generator)
- Material transfer units (if needed, consider the choice between integrated or detached from the main isolator)
Do not design the isolator to have the same footprint as the machine to encapsulate to contain the budget. Design errors can be much more expensive than having extra isolator space.
Do foresee some extra space around the machine to encapsulate so that it is possible to perform side activities like environmental monitoring in a compliant and safe way.
Method
An aseptic isolator’s additional primary role is to decontaminate the internal surfaces where the process takes place. Moreover, the isolator provides a laminar flow area to protect the processing area from particle contamination. These functions can be performed in multiple ways.

Figure 3 – Different method of air supply: technical area vs. cleanroom
The following points need to be considered to identify the specific isolator requirements in relation to methods:
1. Method of air supply
- Air taken from outside
- Air taken from a technical area (impact on the footprint in the technical area)
- Air taken from cleanroom
2. Method of decontamination
- Choice of the decontaminating agent (impact on process and materials)
- Choice of mobile system or integrated system
3. Method of material transfer
- Passive systems: Rapid Transfer Port (RTP) (impact on the process, for example, manual or automatic stopper supply)
- Active systems: Autoclaves, freeze dryers, sterilizing tunnels, disinfectant hatches, electron beam tunnels (significant impact on isolator mechanical integration and logic of pressure cascade)
Do not choose in a rigid way the stopper supply method. Retrofit of features can be disruptive and expensive.
Do onsider flexible choices that allow easy retrofit of beta stopper vessel in case of increase of volumes (RTP installed on removable panel).
Material
Like any pharmaceutical processing machine, it is crucial to specify requirements linked to construction material. Special attention is required as the isolator’s internal surfaces will come in contact with aggressive sporicidal agents.
The material that is processed inside the isolator can have a big impact on some isolator features.
Any production process needs new components to be fed and waste to be removed. Even if the isolator is a barrier technology, it needs to allow this passage of materials to sustain the process without impacting the sterility.

Figure 4 – Example of material transfer inside (via rapid transfer port 1) and outside the isolator (via rapid transfer port 2)
The following points need to be considered to identify the specific isolator requirements in relation to materials:
1. Material of construction requirements
- Compatibility with product
- Compatibility with cleaning agents, sporicidal agents
2. Product to process
- Solution or suspension (impact on the process, recirculation of suspension might require more connections in the isolator wall for product path)
- Toxic or non-toxic (significant impact on the isolator design, higher complexity in the product is toxic)
3. Product requirements
- Product oxidation (consider the need for nitrogen blanketing requirements)
- Product degradation (consider the light requirements, residues of sporicidal agent requirements)
4. Hanging material
- Design of hanging bars and hooks (impact on geometry and quantity of elements)
5. Materials to bring in
- Product path (consider the size, number of parts)
- Stoppers/Closures for vials/syringes (consider the size, quantity, flow properties)
- Consumables (consider the size the size, quantity, package)
6. Materials to bring out
- Product
- Waste (Consider the process: location, size, nature of waste produced and the step when this is produced)
Do not design the isolator if the properties of the product and materials to process are not known. Minor differences can lead to different design choices.
Do onsider the chemical/physical properties of the material to process. In case of automatic stopper supply, consider the material’s flow properties as this might have an influence on the inclination of the isolator wall where the RTP is installed.
Mother nature
The isolator air handling unit can provide a stable set point of pressure, temperature, and humidity. These attributes guarantee that the decontamination and production process can run effectively.

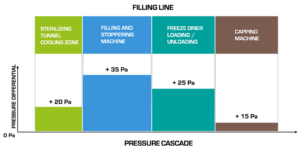
Figure 5 – Example of a pressure cascade between different machines in a freeze-dry filling line
The following points need to be considered to identify the specific isolator requirements in relation to mother nature:
1. Temperature requirements
- Decontamination process (consider the decontamination process requirements)
- High/Low surface temperatures (consider the impact to decontamination process)
2. Humidity requirements
- Decontamination process (consider the decontamination process requirements)
- Process temperature and dew point (essential to keep humidity low to avoid condensation, critical when filling cold products)
3. Pressure requirements
- Differential pressure with cleanroom
- Pressure cascade upstream/downstream machine